Virtual Reality Collaborative environment
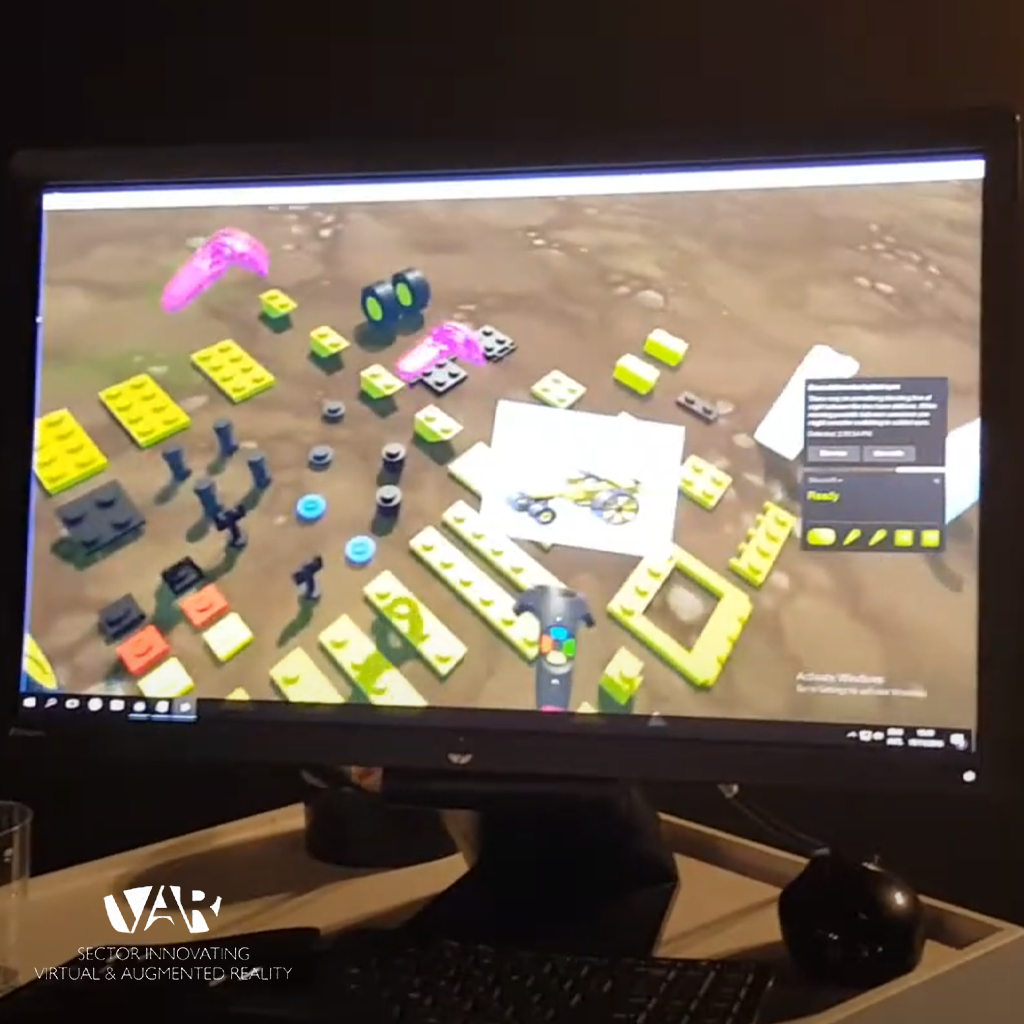
With this concept we want to demonstrate the added value of collaborative training. Again using the Unity game engine, we can have two players, regardless of their physical location, working together in one virtual world. For the prototype, it was decided to let the users assemble a LEGO car together on the basis of a step-by-step plan and productivity tools. Within a professional context, remote training could be provided via this method, independent of the physical location of the users.
Model Based Tracking as communication tool
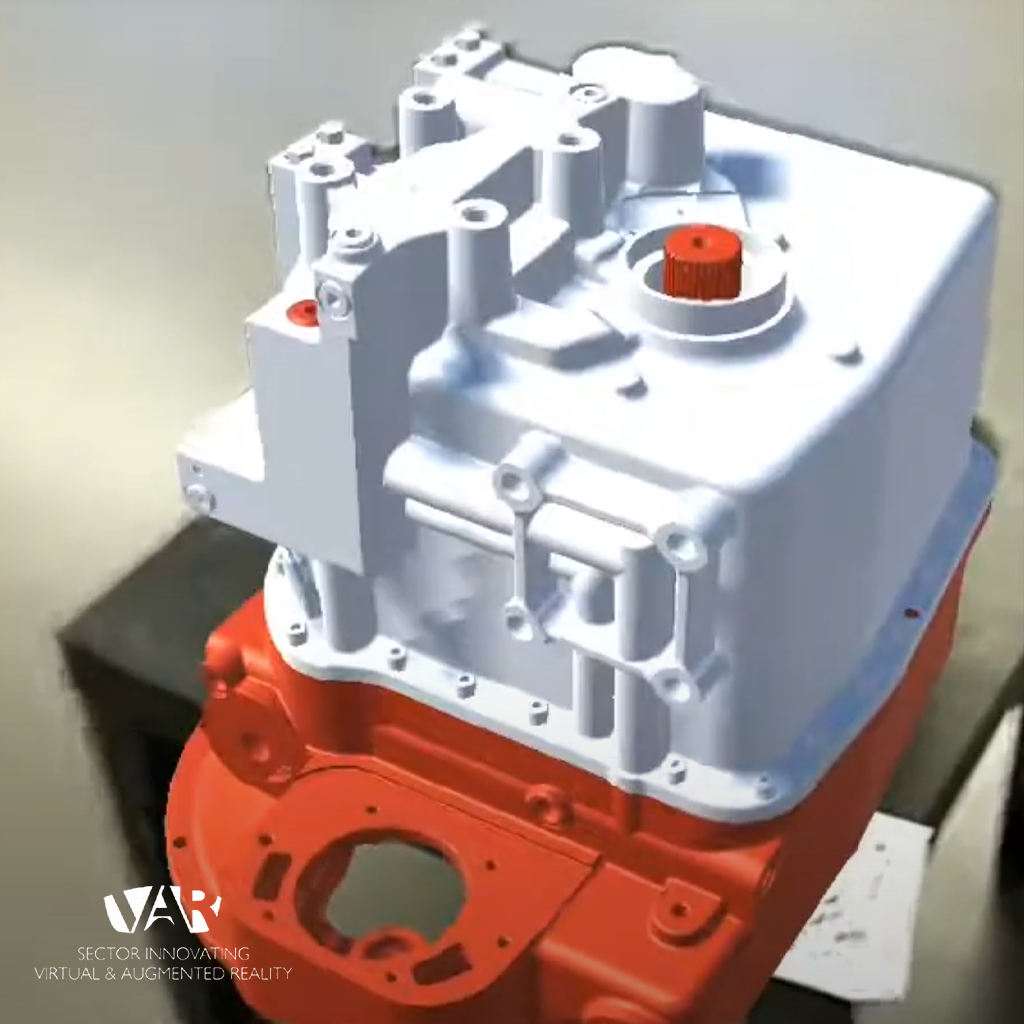
For this prototype, the model-based tracking technology was used to demonstrate the usefulness of the application as a communication tool within a production environment. As a replacement for written tree structure lists, various departments, such as quality check and repair, can display shortcomings on unique assembly pieces in a very visual way. In this way, operators can proceed to repair much faster instead of going over the quality check list manually and having to track down the errors.
Augmented Reality Model Based Tracking
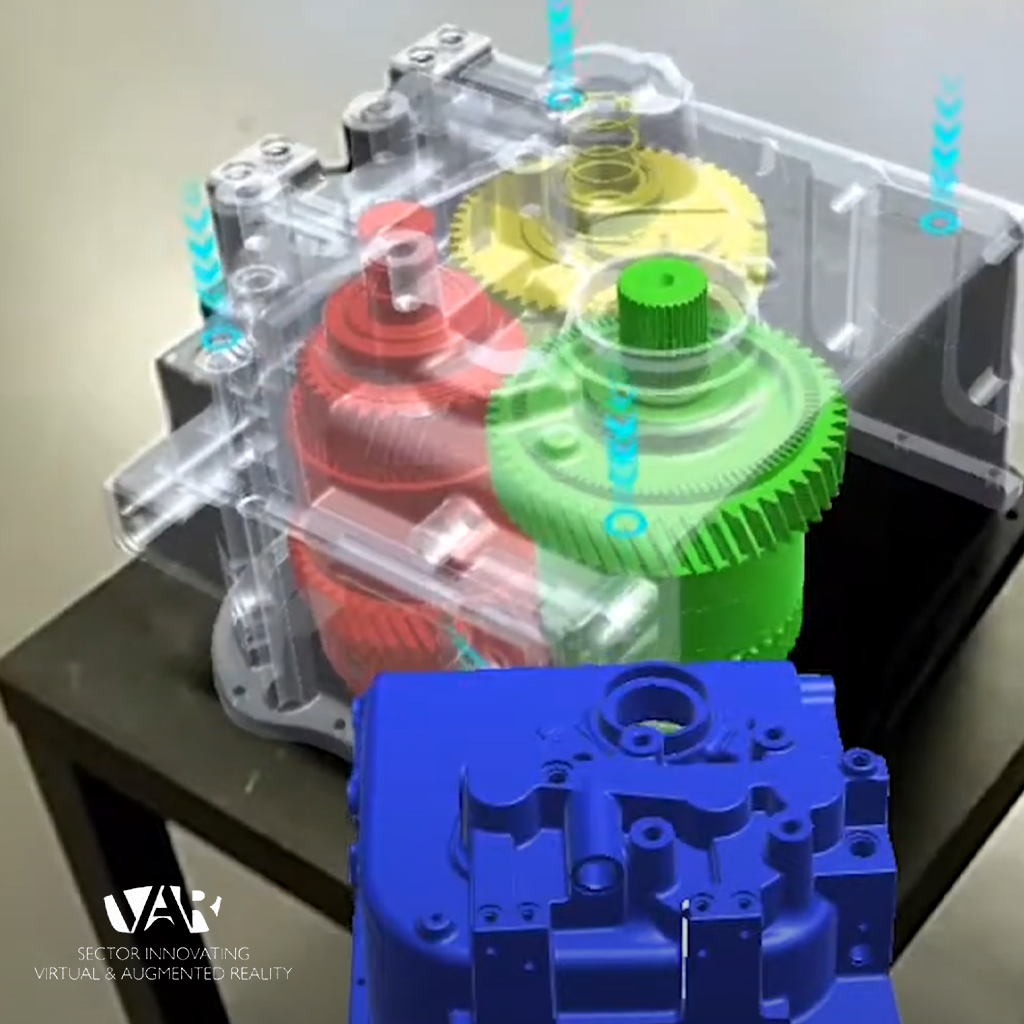
Model-based tracking makes it possible to project augmented reality onto physical objects without the need for trackers or QR codes. This brings the great advantage that the space or physical objects do not have to be adjusted in order to project AR, but also that we can accurately pin the digital information to the physical elements. This prototype shows the potential of model-based tracking in the context of virtual training on physical parts. The user is guided step by step in the real life scenario about the correct assembly steps.
Virtual training: 360° video versus interactive VR
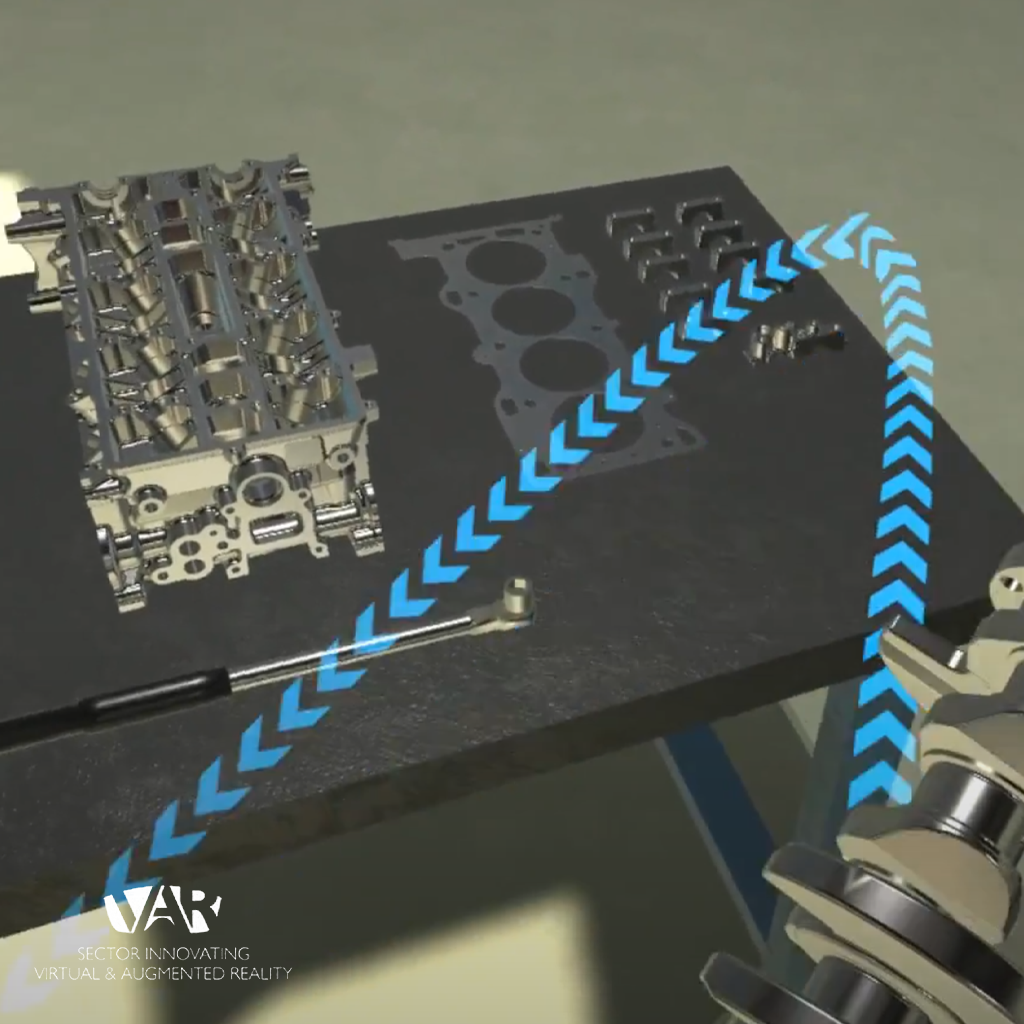
In addition to the developments that are happening in the field of interactive virtual reality, it is also possible to capture an environment using 360° photo and video. In both cases, the user can view the virtual environment using a virtual reality headset. In collaboration with Thomas More and their parallel TETRA project on 360° video, two prototypes were developed where the user can digitally follow the assembly of an engine block. In the first prototype, the user can follow the assembly using a 360° video, in the second, the user can perform the assembly virtually himself in an interactive virtual reality training environment. The intention is to test these two prototypes and compare both methodologies within the new joint TETRA project on ‘Immersive Training’, which will start from September 2018.
Augmented Reality “program by example”
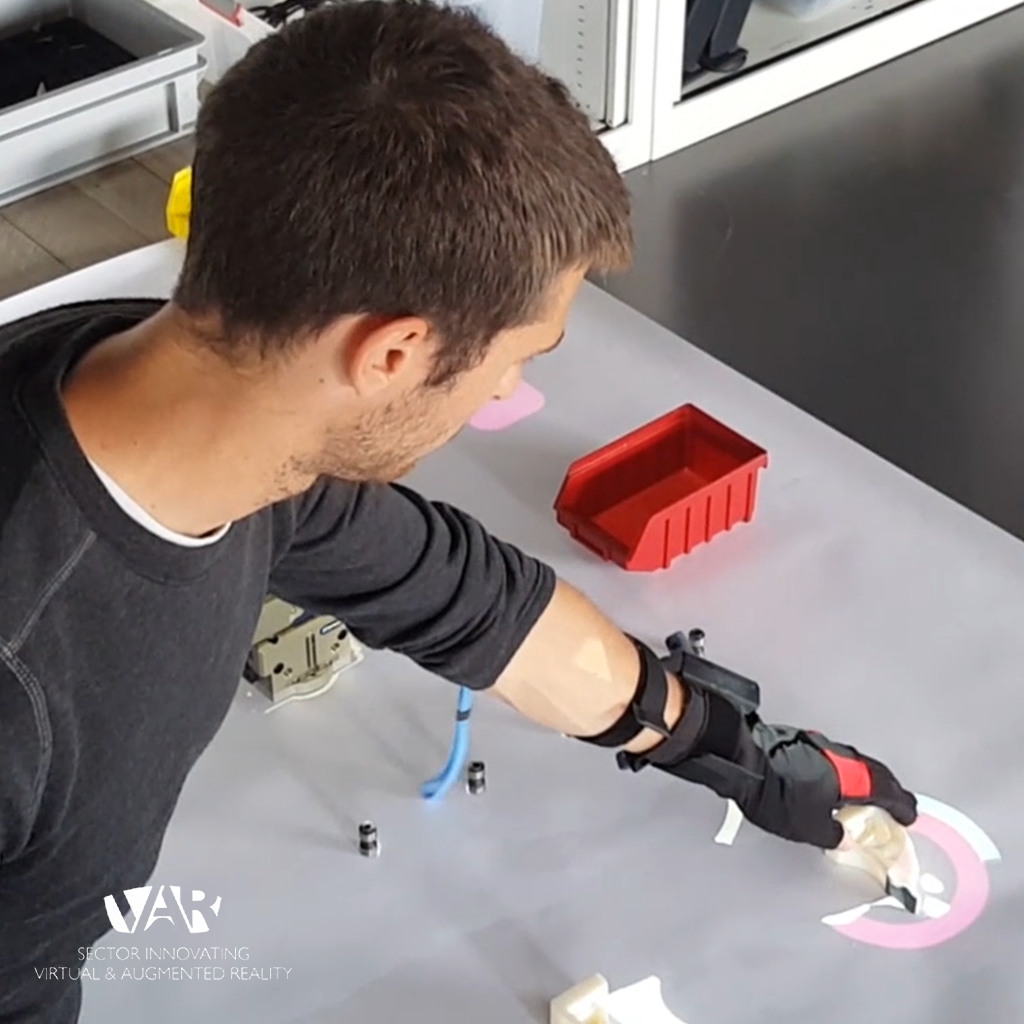
Using projection and a digital replica of the physical parts (digital twin), an operator can be guided hands-free in an assembly. The innovative approach of this method is the way in which the projected procedures are captured. They are generated dynamically by first performing the assembly yourself within a teaching mode – program by example. Each step in this proof-of-concept is linked to CAD matching and/or image processing integration to guarantee that the individual parts are also correctly oriented during assembly.
Virtual link: watch cross-platform in VR
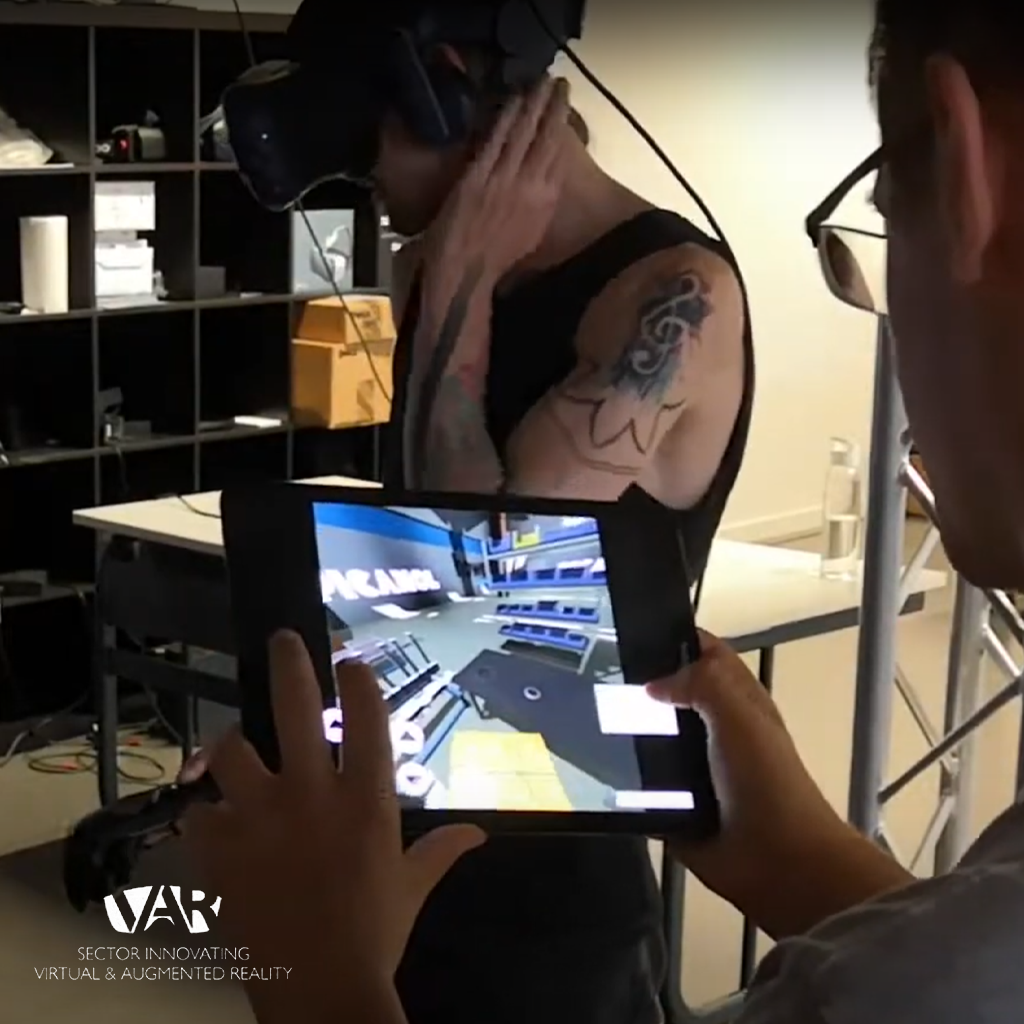
We developed a collaborative platform with the Unity game engine with which a supervisor can support the person wearing a virtual reality headset with his tablet or smartphone. We have the option to watch from a first person perspective or to choose a position in the virtual space. This prototype shows how we can easily interact with multiple users within an isolated experience such as virtual reality, even without having to wear a headset.
Augmented Reality indoor wayfinding
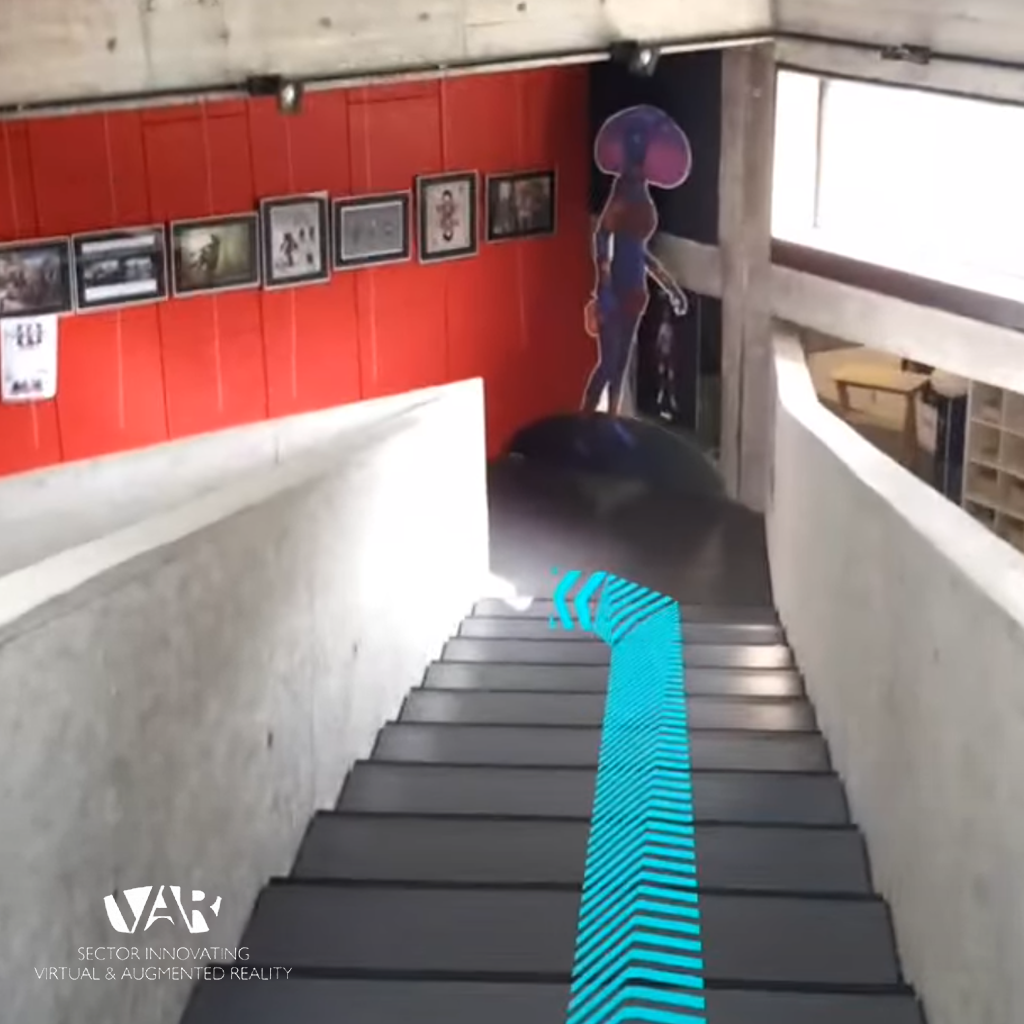
In indoor wayfinding, the lack of a GPS signal and/or usable WiFi signals presents a challenge to help someone navigate from point A to point B without using extra hardware such as beacons. Commercial hardware such as the Samsung S8 was used for this, combined with the ARcore framework, with which a prototype was developed that makes indoor wayfinding possible. The user can select his target location from a central point, after which he is guided visually step by step.
Virtual Reality Training: Picanol Case
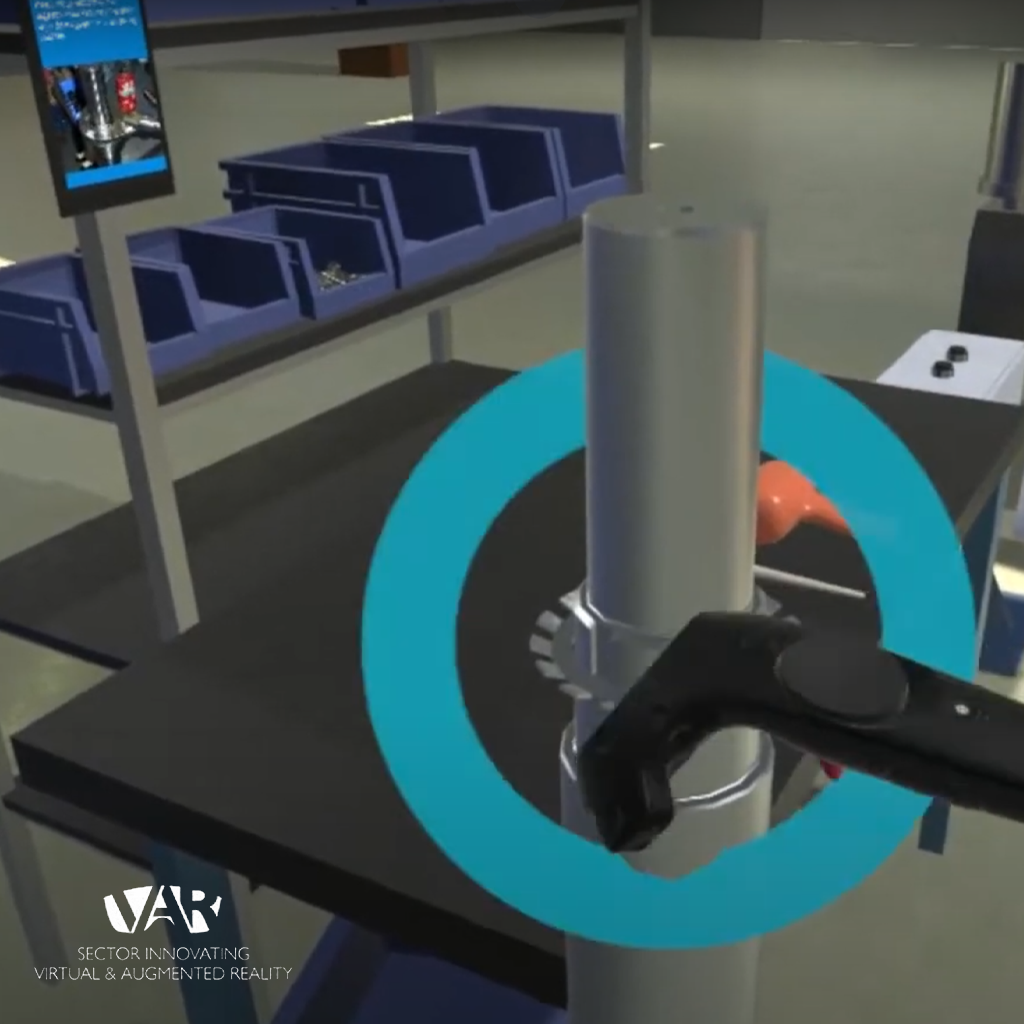
Together with Dana, Picanol, CNH industrial, Barco and Cronos aan de Leie, game technology was brought in to investigate a new form of training. A combination of a scanned working environment, cad models and an interactive game engine made it possible to prototype a Virtual Reality Training framework. Employees can learn to assemble virtually using a ‘digital twin’ of the production line. Here you can see a video of the VR training framework in action based on a part of a loom at Picanol.
Virtual Reality Training: Dana Case
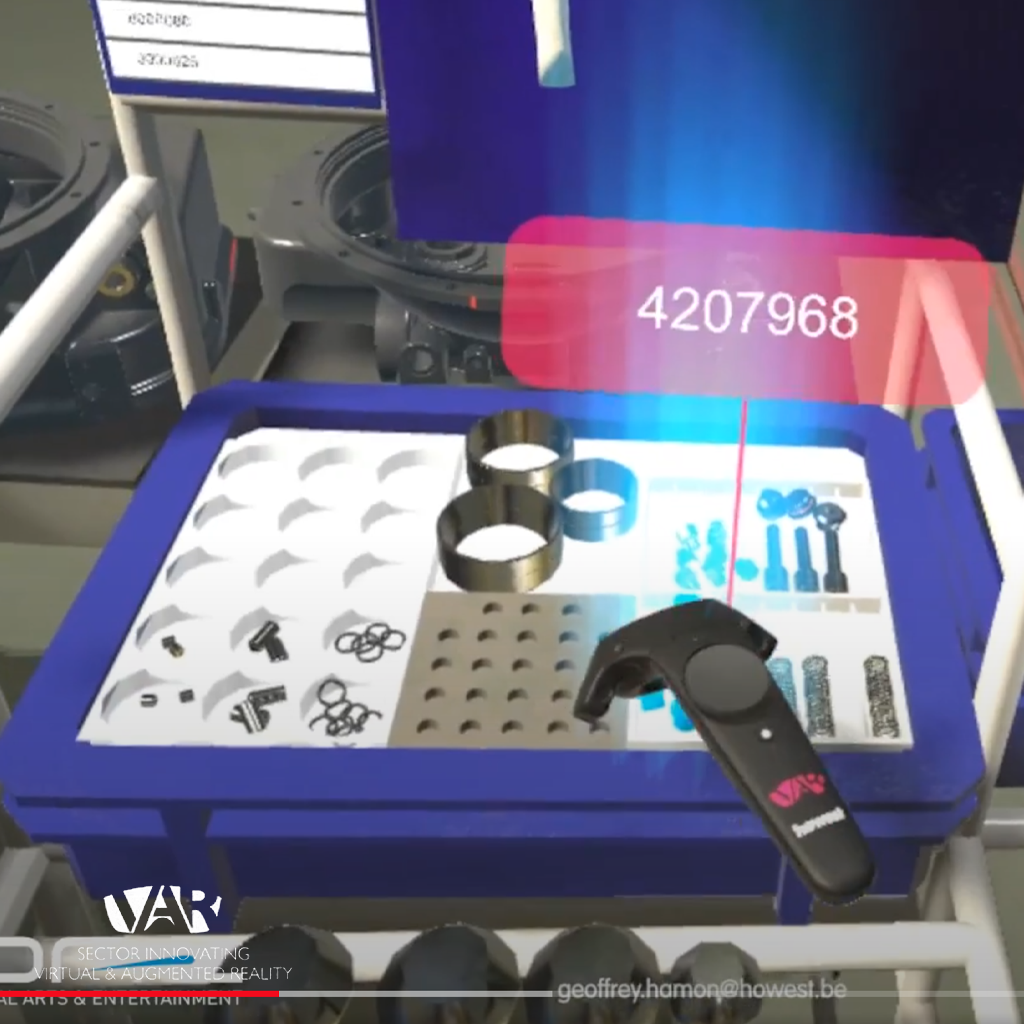
Together with Dana, Picanol, CNH industrial, Barco and Cronos aan de Leie, game technology was brought in to investigate a new form of training. A combination of a scanned working environment, supplied cad models and an interactive game engine made it possible to prototype a virtual reality training framework. Employees can learn how to assemble virtually using a digital twin of the production line.
SIVAR
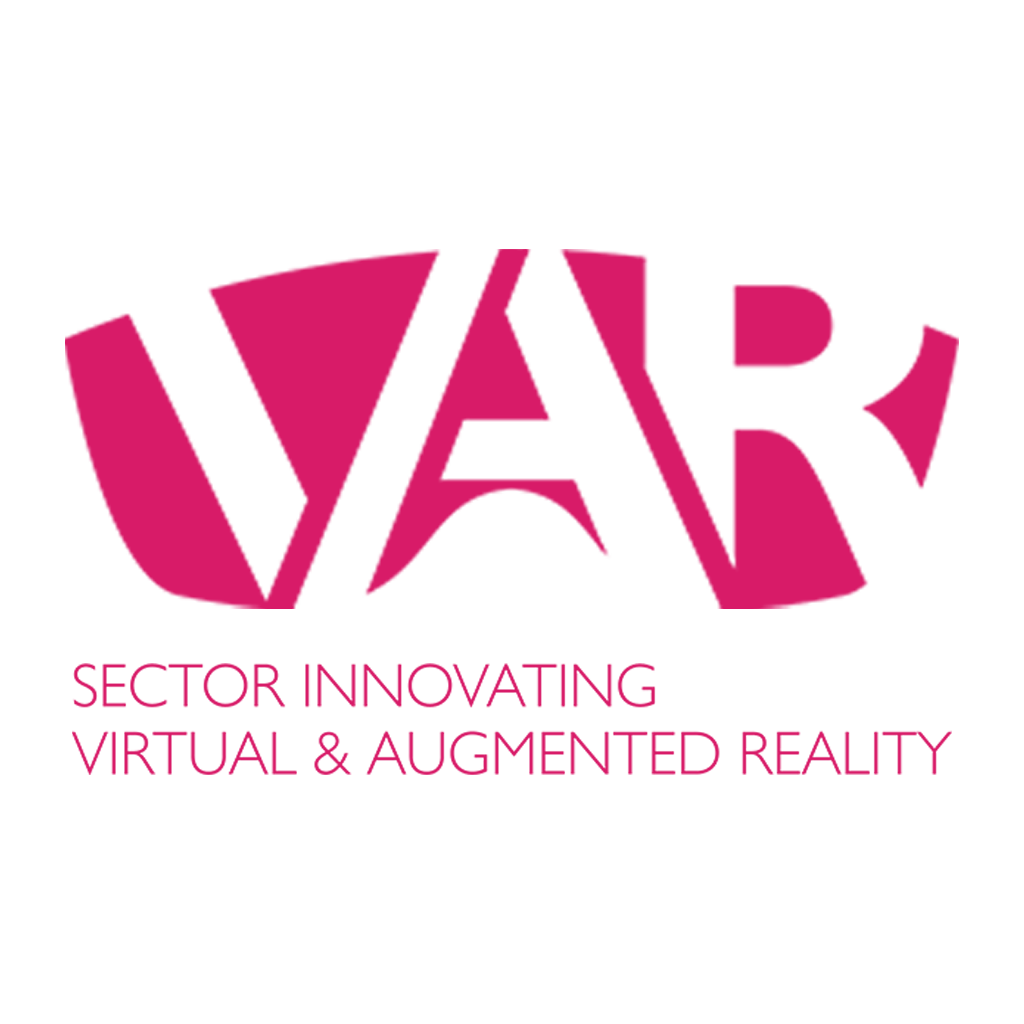
With this “Sector Innovating Virtual & Augmented Reality” project, partners and external organizations are guided in defining this added value in their current workflow. The project consists of two parts: a first part aimed at developing concrete proofs of concept where VR and AR technology is applied within the industrial sector and a second part aimed at a broader knowledge transfer for partners from other sectors.
SIVAR Slotevent
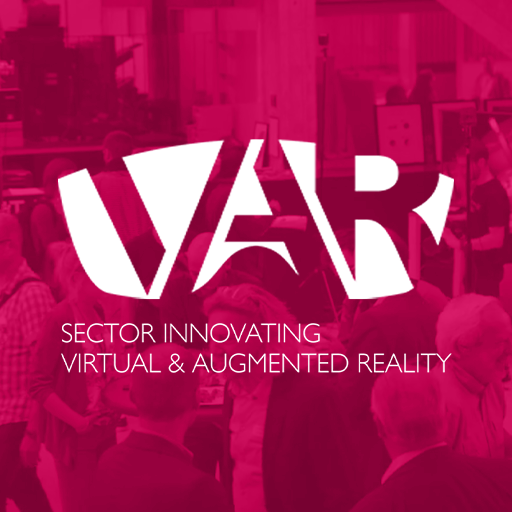
With this “Sector Innovating Virtual & Augmented Reality” project, partners and external organizations are guided in defining this added value in their current workflow. The project consists of two parts: a first part aimed at developing concrete proofs of concept where VR and AR technology is applied within the industrial sector and a second part aimed at a broader knowledge transfer for partners from other sectors.