Virtual Reality Collaborative environment
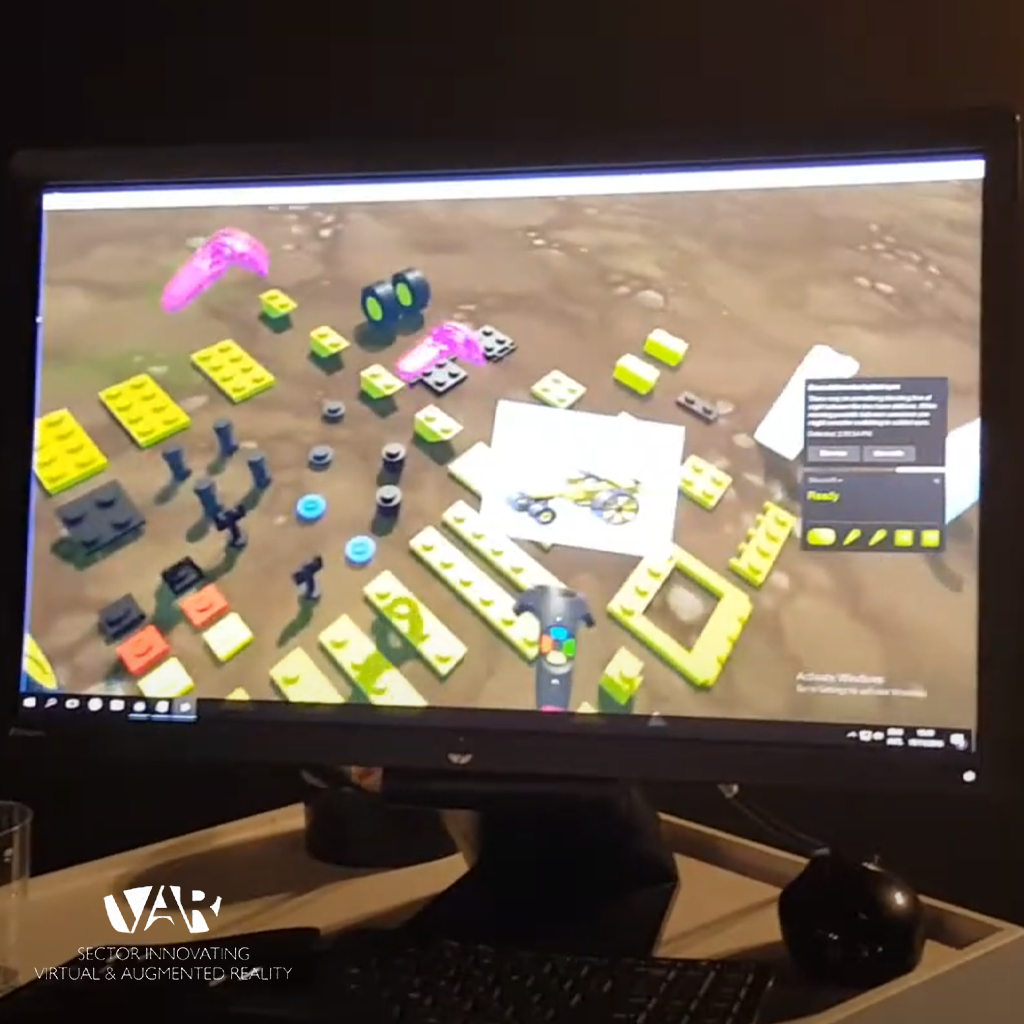
With this concept we want to demonstrate the added value of collaborative training. Again using the Unity game engine, we can have two players, regardless of their physical location, working together in one virtual world. For the prototype, it was decided to let the users assemble a LEGO car together on the basis of a step-by-step plan and productivity tools. Within a professional context, remote training could be provided via this method, independent of the physical location of the users.
Virtual training: 360° video versus interactive VR
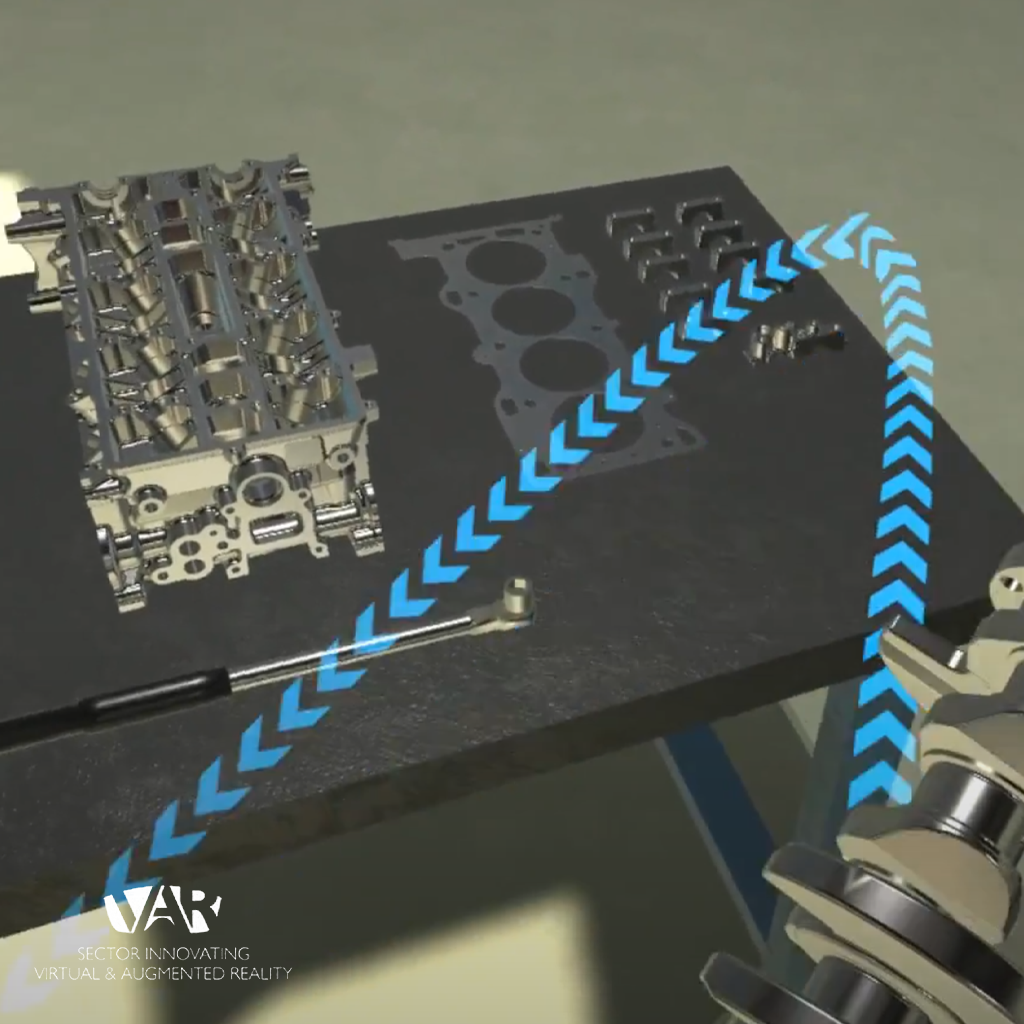
In addition to the developments that are happening in the field of interactive virtual reality, it is also possible to capture an environment using 360° photo and video. In both cases, the user can view the virtual environment using a virtual reality headset. In collaboration with Thomas More and their parallel TETRA project on 360° video, two prototypes were developed where the user can digitally follow the assembly of an engine block. In the first prototype, the user can follow the assembly using a 360° video, in the second, the user can perform the assembly virtually himself in an interactive virtual reality training environment. The intention is to test these two prototypes and compare both methodologies within the new joint TETRA project on ‘Immersive Training’, which will start from September 2018.
Augmented Reality “program by example”
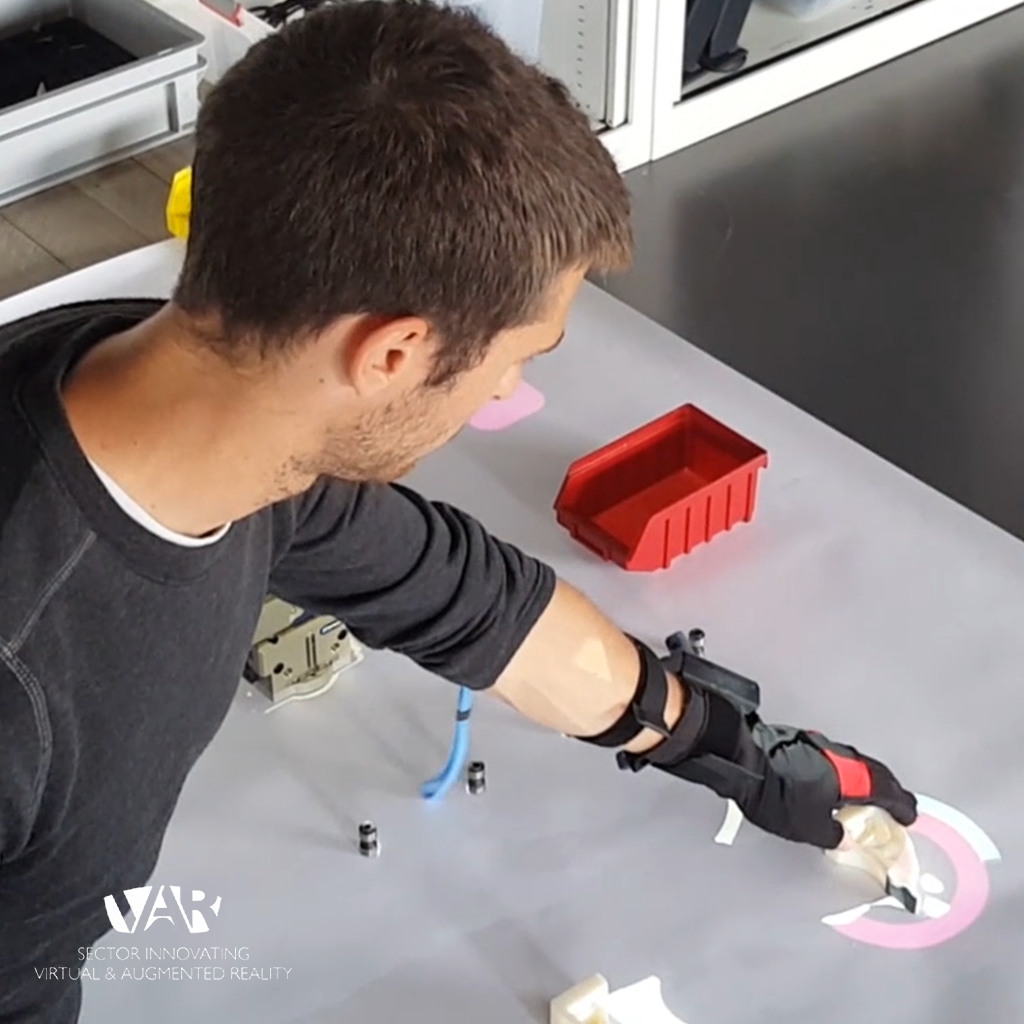
Using projection and a digital replica of the physical parts (digital twin), an operator can be guided hands-free in an assembly. The innovative approach of this method is the way in which the projected procedures are captured. They are generated dynamically by first performing the assembly yourself within a teaching mode – program by example. Each step in this proof-of-concept is linked to CAD matching and/or image processing integration to guarantee that the individual parts are also correctly oriented during assembly.
Virtual Reality Training: Picanol Case
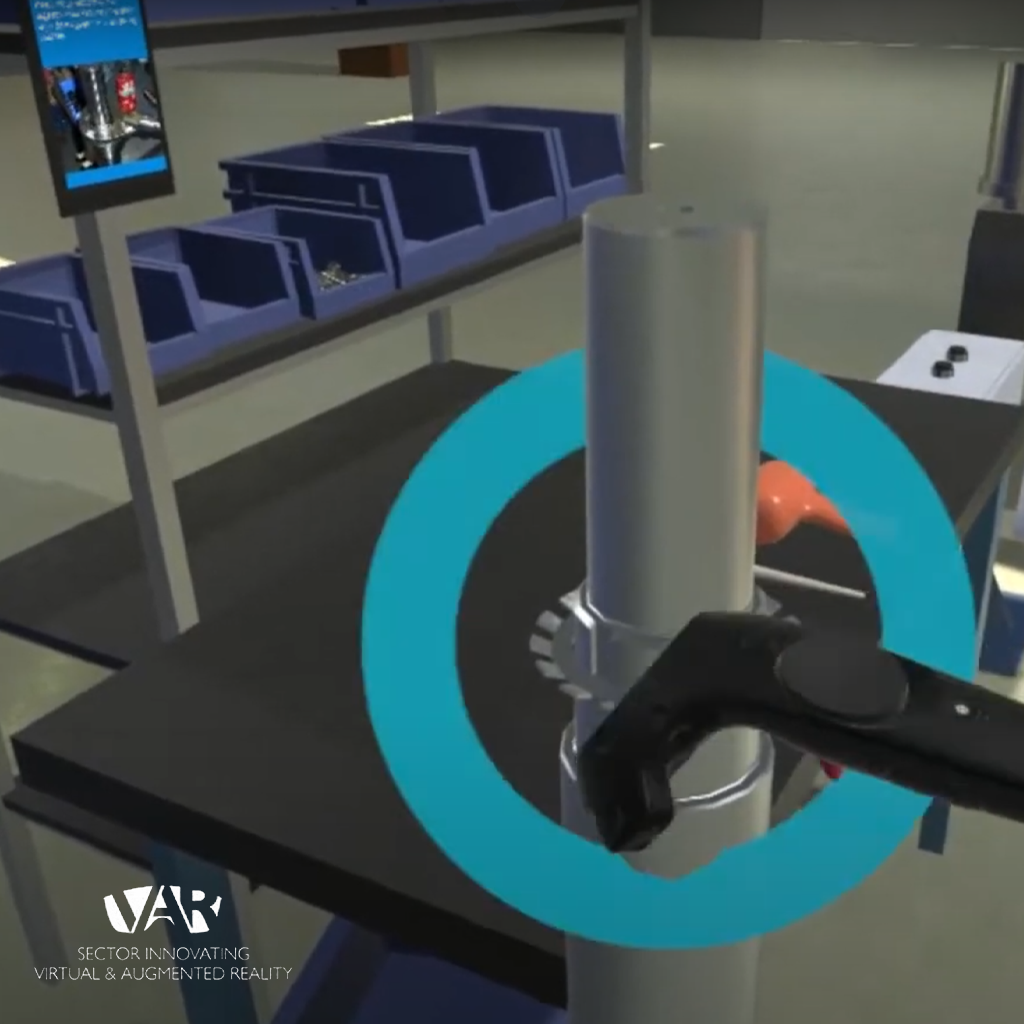
Together with Dana, Picanol, CNH industrial, Barco and Cronos aan de Leie, game technology was brought in to investigate a new form of training. A combination of a scanned working environment, cad models and an interactive game engine made it possible to prototype a Virtual Reality Training framework. Employees can learn to assemble virtually using a ‘digital twin’ of the production line. Here you can see a video of the VR training framework in action based on a part of a loom at Picanol.
Virtual Reality Training: Dana Case
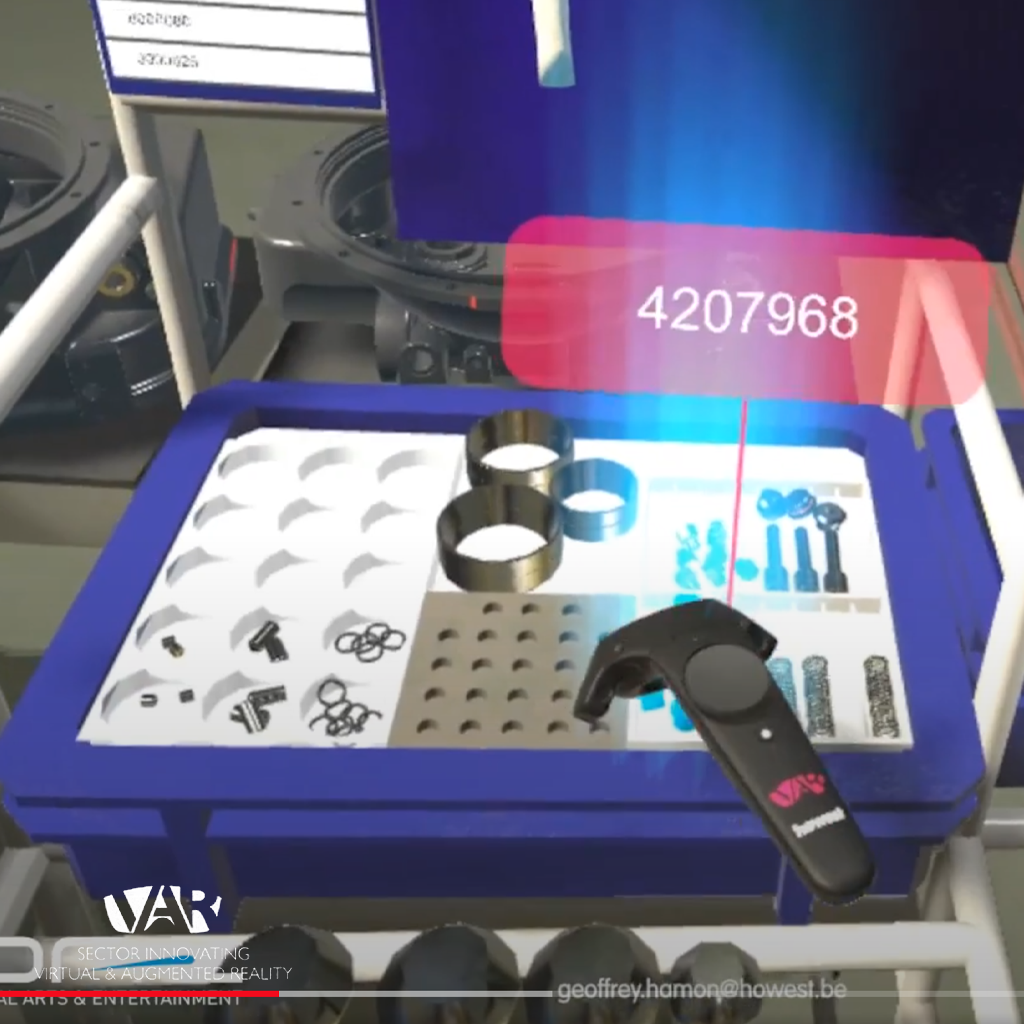
Together with Dana, Picanol, CNH industrial, Barco and Cronos aan de Leie, game technology was brought in to investigate a new form of training. A combination of a scanned working environment, supplied cad models and an interactive game engine made it possible to prototype a virtual reality training framework. Employees can learn how to assemble virtually using a digital twin of the production line.